Production Planning for Major Projects- Lean in Construction Industry
After observing Toyota’s production line, Ohno identified seven types of waste. As shown in Table 1-1, the 7 types of wastes are listed along with comparable examples in construction and design. Observation comments are made for more clarifications.
Table 1-1: Ohno's Seven Types of Waste with Examples from Construction
Types of Waste (Ohno 1988) | Examples of Wastes in Construction and Design (Abdelhamid et al. 2008) | Observation |
Overproduction | Excess materials of concrete or asphalt Over-excavation Design scope creep | Common occurrence in the construction industry |
Inventories | Storing raw materials at site Holding work in progress | Causing storage cost, space limitation, security, safety, and environmental challenges |
Over-processing | Painting internal walls of an underground utility tunnel Design scope elegance | No value added |
Defects | Non-conformance to quality in construction and design | Resulting in rework |
Unnecessary motion | Movement at site | Lean logistics plan to minimize unnecessary movement and transportation |
Unnecessary transport | Double handling of materials Transportation of workers to/from labour camp to field and to/from break area | |
Waiting | Idle equipment Designer awaiting owner approval Workers waiting for work or work waiting for workers | Typical type of waste in construction industry |
The construction industry lags behind manufacturing with respect to efficient use of resources, productivity, and quality (Eastman and Sacks 2008). Client decision-making, design management, and construction management are considered endemic challenges in contemporary construction projects (Koskela 2000). The Lean approach focuses on improving the value stream and flow of processes by eliminating waste (Koskela 1992). Waste is any activity or condition that does not add value to internal or external customers.
Table 1-2 reviews two efforts to identify waste or unproductive time. Despite the different observation methods, they are surprisingly similar (Ohno 1988; McTague and Jergeas 2002).
Table 1-2: Comparison between McTague and Jergeas (2002) and Ohno (1988)
Unproductive time (McTague and Jergeas 2002) | 7 Types of Waste (Ohno 1988) | Observation |
--- | Overproduction Inventories Over-processing Defects | Minor contrast as Ohno’s observation was on the process and the product while McTague and Jergeas focused on the process only |
Late start / Early Quit (3%) Instructions (6%) Tool and Materials (5%) Personal Breaks (4%)
| --- | |
Traveling (12%) | Unnecessary motion | Concepts match |
Transporting (5%) | Transport | |
Wait and Idle (32%) | Waiting |
The project team in Construction Package 5B (CP5B) at Lusail City applied many initiatives of Lean construction to eliminate waste and generate value. For example, the rebar installation of the underpass wall structure (1,018 m long). Forty segments of the underpass wall, out of 108 segments have an average height of 14 m, which is 6 m higher than maximum height ever constructed in Qatar. The GC applied rebar prefabrication methodology by using a huge rebar cage on the ground and lifting it up to its final position on completion of the assembly process. This Lean Construction initiative reduced the cycle time of rebar installation from 30 to 19 days for each segment. Productivity was greatly increased, and operations were much safer than under the conventional rebar assembly method. Quality achieved the highest standards, construction cost was optimized, and the delivery of this part of the work was ahead of schedule.
The Lean production philosophy in manufacturing has been used to plan and execute many construction projects. However, applying such a paradigm to the construction of MPs would be very challenging due to the difficulty of ensuring a high level of integration in these complex operations. For example, in the mega-project referenced earlier that inspired this research (CP5B), it was found that the available Lean production planning and control solutions cannot be applied directly to address integration challenges of MPs.
Lean Construction was followed closely by the introduction of the LPS® (Ballard and Howell 1994). LPS® is Lean Construction’s production planning and control system. The underlying reasons behind developing LPS® include:
· produce practical plans that can be utilized at the production level.
· address the shortcomings in traditional common approach and its inability to build consensus amongst project stakeholders and support the site’s day to day project execution efforts.
· realize the inherent principles of Lean Construction to minimize waste and maximize value.
Article or Post Details
2021-08-07
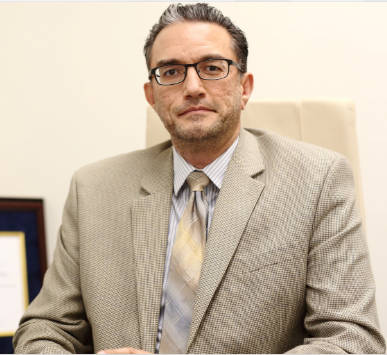
Dr. Luai M. El-Sabek