Production Planning of Mega-Projects in Lean Construction- Introduction
Many owners and government agencies mandate the use of critical path method (CPM) as a contractual requirement (Senior 2009). Common practice in Mega-Projects (MPs) in Qatar and most Middle East countries is to submit the fully detailed baseline schedule, always CPM based software, within 14-28 days of the project start date. This schedule is detailed to very short durations of execution activities. Detailing the schedule in the first few weeks of a three-year mega-project to the production level with no input from site and trades’ teams relies heavily on assumptions and forecasting all elements.
A review of 16 delay studies conducted in 12 developing countries found that ineffective planning and control were contributing factors in 87% of the cases where projects fell significantly behind schedule (AlSehaimi et al. 2013). Similarly, the percent plan complete (PPC) is typically below 50% in construction projects experiencing delays. The PPC metric measures accomplished work against the commitment or planned work (Ballard and Howell 1998a). PPC was the first metric to measure and show the disconnect between production control and project planning.
MPs are unique for having mega relationship networks among project stakeholders, with significant impacts on communities and the environment. As confirmed by industry experts, delays and budget overruns are serious problems of MPs; these delays could be compounded by the production planning and control tools used. Changes to schedule, budget, and scope, as well as an inadequate quality of design are identified as the most challenging factors affecting the integration and delivery of MPs (El-Sabek and McCabe 2017).
Traditional construction management is based on the transformation concept, converting inputs to outputs (Koskela 1999). The baseline schedule is typically created using the CPM and sequenced according to a lengthy list of unpredictable but forecasted construction processes, variable productivity, and unknown unknowns (Abdelhamid et al. 2008). Often mega-projects are managed by planners and other professionals without deep domain experience (Flyvbjerg 2014). The resulting baseline schedule may not address how activities will be executed nor consider maximizing value or minimizing waste-principles inherent in Lean Construction (Koskela et al. 2002). With the commencement of construction activities in the traditional approach, management often transfers its focus to control efforts disconnecting project planning from execution (Ballard and Howell 1998b).
The traditional approach to planning assumes that the construction team is capable of handling production variations at the site, and that all the required resources are available. Site operations are driven by a top-down push system, where lookahead and weekly plans are filtered from the detailed baseline schedule (Tommelein 2015). This model ignores the actual status of the work on site. Previously developed, often outdated plans are forced on construction team for execution. This results in an imbalanced system leading to execution failures with unmet commitments and delays (Abdelhamid et al. 2010; Koskela 1999). If the prerequisite work is not ready, workers and/or equipment have to wait, resulting in unnecessary waste. Similarly, if an activity requires fewer resources than are assigned to the system, the result is also undesired waste due to surplus workers and/or equipment. Both negatively affect the overall project performance. The growing awareness of failures in achieving time and cost targets motivated the development of alternative solutions (Ballard and Tommelein 2016).
One of these alternatives is the Last Planner® System (LPS®), which was touted as a new production planning and control method that complements CPM by addressing some of its shortcomings at the production level (Ballard and Howell 1994). The LPS® is structured in four phases (Ballard 2000):
Master Schedule (Needs to be done): | Major milestones are defined (using CPM) |
Phase Schedule (Should be done): | Detailed plan of one phase of master schedule showing dependencies between activities (using CPM) |
Make-Ready Plan, MRP (Can be done): | Rolling plan from 3-6 weeks (using new processes) |
Weekly Work Plan, WWP (Will be done): | Commitments are made and measured (using new processes) |
Throughout these systematic phases, the LPS® creates an environment that facilitates cooperative discussion, debate, and rapid learning (Howell et al. 2011). The aim of production planning and control is to embrace a new philosophy rather than direct the project team on what to do. The team cooperatively decides how members will coordinate and improve workflow to reduce the gap between DID and WILL. The result of this process is higher productivity, more predictable workflows, a greater degree of team-building, respect, and reliable delivery of tasks (Ballard and Tommelein 2016).
LPS® provided the author with hope that mega-projects can be better managed. A mega-project typically comprises multiple subprojects located throughout a large area, with each subproject responsible for its own reporting. LPS® can be applied to each subproject using best practices already common in the industry. However, the challenge exists in the gaps between these subprojects so that aggregated production control and integration can be achieved at the mega-project level. The larger the project, the greater the number of subprojects and gaps between them, and the greater the potential for gaps to result in significant problems for the overall project.
Article or Post Details
2021-08-07
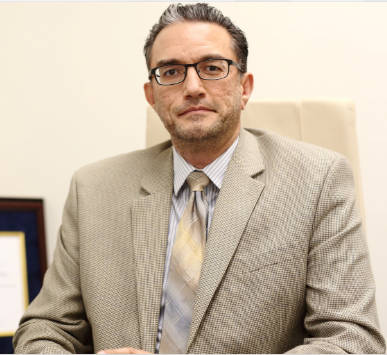
Dr. Luai M. El-Sabek